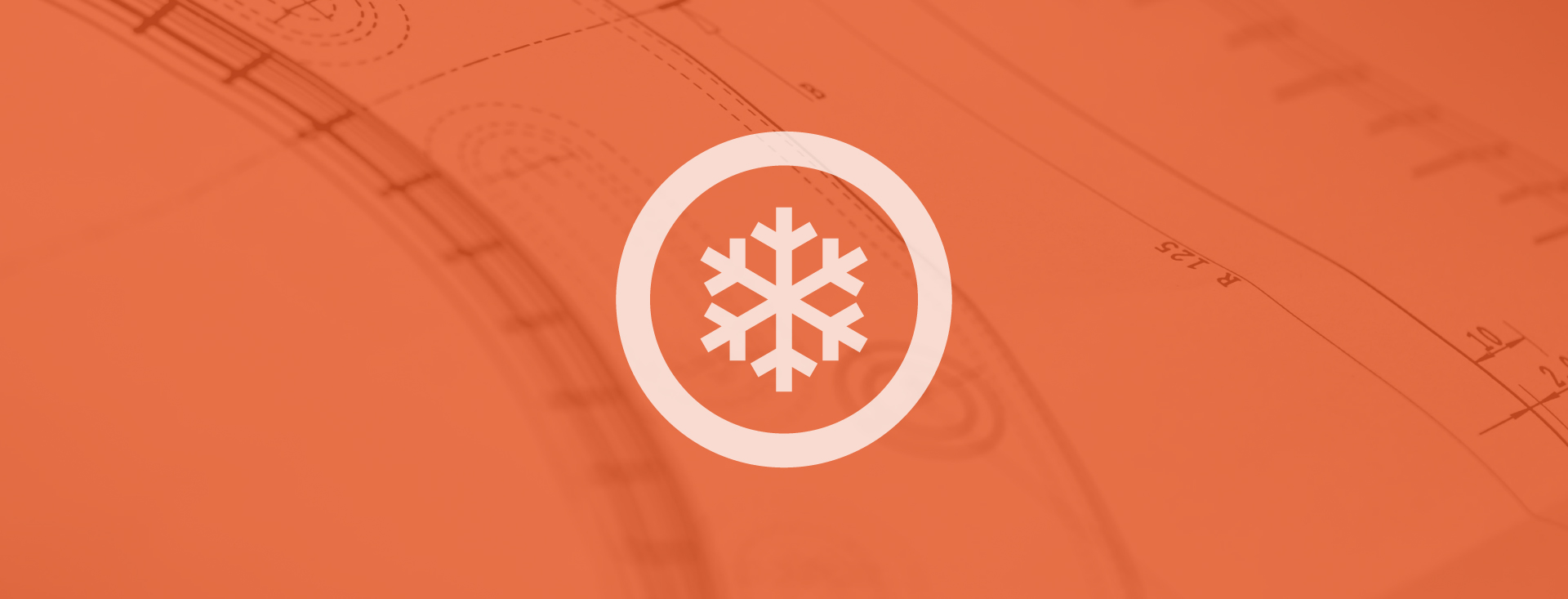
Innercore Extra Cooling System
The Innercore Extra Cooling System is a technology covered by an exclusive patent which is the result of extensive planning and development work which lasted many years; this system allows the cooling down of truncated cone-shaped moulds.
The Innercore Extra Cooling System allows to stratify the control of the temperature and the effect of the cooling system inside and all along the punch. It also allows to optimize all the cooling conditions, to save resources, to reduce the wear of the machine and its energy consumption, thus ensuring a longer life both to the mould and to the machine.
It is mainly used in the moulds for truncated cone-shaped products from 3l. to 50l.
This cooling system is able to:
-
Stratify the control of the temperature and the effect of the cooling system inside and all along the punch.
-
Optimize all the cooling conditions as well as save resources.
-
Reduce the mass of the punch in order to reduce the wear of the machine and its energy consumption thanks to a lower inertia.
Apart from the use of qualified materials, the major effects of this technology are:
-
A gain of about 20% in the cooling time.
-
A better filling of the mould as a result of the different temperatures in the material flow.
-
A longer service life for the mould and the machine.
-
Energy savings.
Thanks to the Innercore Extra Cooling System technology, Abate is able to offer better cooling performance and cycle times than most mould makers of truncated cone-shaped containers.
Here are some examples (mould for buckets/ round containers):
30 l. bucket designed for up to 10 million pieces (*), with a cycle time of 14 sec.(*).
20 l. bucket designed for up to 10 million pieces (*), with a cycle time of 12 sec.(*).
10 l. bucket designed for up to 10 million pieces (*), with a cycle time of 6 sec.(*).
3 l. bucket designed for up to 10 million pieces (*), with a cycle time of 4.9 sec.(*).
(*) – Obtained with the best configuration of the mould, moulded by using PP and top-fast IMM machine for packaging and with defined conditions for cooling and wall thickness.
Processes
Thanks to its technology, flexibility and analytical approach, Abate Basilio does not only manufacture high performance moulds for the injection of plastic materials, but also provides customized solutions for any project. Thanks to the control of the entire production chain, from planning to delivery, each mould ensures unique quality, durability and performance.
Analysis
and planning
Abate offers a service of consultancy and analysis of the customer’s needs specific for each project. A specific technical knowledge is required for each sector, from food industry to chemicals, logistics etc., in order to be able to design and manufacture the more appropriate mould for a specific product.
Construction
and testing
Our production line includes 5-axis machining centres with fully automatic tool and pallets changers which allow us to achieve maximum repeatability and quickest throughput. Our machines are equipped with a laser control of the real dimensions directly obtained during the process in order to achieve the maximum precisions.
Maintenance
and after-sale
Our technical department ensures a fast, reliable and precise after-sale service. 95% of the company production is destined to be exported to different countries located over 5 continents. Our company has always given support to customers all over the world thanks to reliable planning of the mould and availability of spare parts which are guaranteed for 20 years.